The History of Bicycle Helmets
By Randy Swart, Executive Director
Bicycle Helmet Safety Institute
Summary: This is a page of oral history on helmets, just one man's recollection of how bicycle helmets developed.
In the beginning, there were injuries. From cycling's earliest days there were head injuries. As more roads were paved it is likely that the head injuries increased, since macadam and asphalt are completely unforgiving as crash surfaces. In the 1880's high-wheel users in clubs saw that head injuries were a problem and began using pith helmets. Pith is a crushable material, and was likely the best material available at the time. Although it would probably break up on impact, there were few cars on the roads, so riders needed protection only against a single impact.
Around the turn of the century racing cyclists began using "helmets" made of strips of leather-covered padding,
initially with a ring of leather around the head and a wool ring above that. Then the style evolved and the ring of
leather around the head was supplemented by strips of leather arranged longitudinally on the head. When I started racing
in the 70's we called them "hairnets" and the nicest ones were made in Italy of beautiful soft leather. By then the interior of the strip was a foam, but it wasn't very protective.
They also rotted from sweat. I asked the more experienced racers if the hairnet we were required to use in races was
protective, and they said "they don't help at all in the initial impact, but they keep your ears from being ground off
while you're sliding over the pavement." Years later lab testing showed that their assessment from field experience was
exactly correct.
By the early 1970's club and racing cyclists with shared experience could see that the injuries that were the worst and the major cause of death were head injuries. We could also see that a helmet could do a lot of good. Some riders just ignored that, as they do today. Others began using hockey helmets. Still others turned to the plethora of headgear on the market, including "bump caps" and others that were more illusion than protection.
The Snell Foundation had promulgated the first bicycle helmet standard in the U.S. in 1970, but at the time only a
light motorcycle helmet could pass it, and that meant two pounds of unvented helmet. Very few, if any, helmets were certified to it, and none made their way to bike shops. Since there was no
commonly used standard, there was no way for the consumer to find out which helmets were most protective.
In 1974 the Washington Area Bicyclist Association despaired of finding information on the relative protection of
helmet brands and formed a Helmet Committee to collect data from ride testing. WABA procured helmets from many sources
and began a series of ride tests. At that time we found that the helmets on the market mostly had some kind of shell with
a squishy foam liner. None had crushable EPS (picnic cooler) foam until the Bell Biker (below) and the Mountain Safety
Research bike helmet came to market in the mid-1970's. Bike club
experience quickly showed that both were far better in performance than the others on the market
The MSR bike helmet was an adaptation of their mountain climbing helmet. It had EPS foam in a ring around the headband, with the top protected to a lesser extent with a suspension system whose nylon straps attached to the shell with deformable hooks. Curves in the hooks were designed to straighten out on impact as an energy management technique. In a few months MSR apparently realized that the suspension system was less effective than the foam section, and that riders impact all over the helmet. They provided EPS glue-on pads to go in the upper area, with a wedge-shaped EPS section between each of the nylon straps of the suspension system. The shell of the MSR was a stiff polycarbonate, probably GE's Lexan.
The Bell Biker also had a hard Lexan shell, and it had a full EPS liner. When it was introduced other manufacturers eventually followed Bell's lead and this type of helmet dominated for a decade. There were still some helmets produced with hard shells and squishy foam liners by Pro-Tec and others, and a notable design called the Skid Lid with strips of hard shell backed by squishy foam.
In the early 1980's Dr. George Snively of the Snell Foundation agreed to work with WABA's helmet committee to provide
us with helmet testing. We procured the helmets, did a ride test, and shipped them to Snell, where Dr. Snively tested
them for strap strength and impact protection in Snell's lab. Snell maintained a strict division between their
certification testing and the testing they did for us. By that time there were 20 or so helmets to be tested, and the
testing showed that the Bell Biker, and updated MSR and a helmet known as the Bailen Bike Bucket (below) were the best of
the lot. The Bailen was the first "one size fits all" bike helmet, with
an adjustable ring inside that fit sizes 6 7/8 to 8. It had no vents, and both internal and external hard shells.
Dr. Snively gave generously of his time and unparalleled expertise to educate the WABA testers in helmetry and helmet standards. WABA's Tom Balderston wrote up the findings and Bicycling Magazine published them--in the face of lawsuit threats from manufacturers--in 1983. That article was a landmark, and alerted consumers to the vast differences in performance between helmets on the market. It helped pave the way for standards to develop.
In 1984 the ANSI headgear committee adopted ANSI Z80.4, the first workable bike helmet standard for the US. The Snell Foundation revised their own standard the next year to adjust the requirements to more realistic levels for bicycle riding impacts. In just a year or so the junk that could not meet the ANSI standard was swept from the market, in some cases by lawsuits. Mid-1980's bike helmets were characterized by EPS foam liners, with ABS or polycarbonate hard shells. Virtually all of them had a simple strap design shaped like a Y on each side. For buckles, most had d-rings or plastic buckles made by Fastex.
In the early 1980's the next big step in bicycle helmet design occurred when Bell introduced their "L'il Bell Shell"
infant-toddler design. To make the helmet lighter, Bell dropped the
outer shell, producing a thick all-EPS helmet that was highly protective. The design was actually an adaptation of a
helmet Bell had produced for pediatricians to protect child heads after surgery. Bell limited the idea to toddler helmets
in the belief that adult helmets would always require a hard shell. In 1986 a designer named Jim Gentes designed an adult
bike helmet with some vents and no shell, and formed Giro Sport Design to market the concept. The lighter weight was an
instant hit, and Giro began selling large quantities of the helmets to racers and others who could afford the high price.
Giro used an outer cover of thin lycra cloth. The cover was hand sewn in the
US and was one of the major costs of producing the helmet.
The all-EPS helmets that followed soon distinguished themselves as protective helmets that had an unfortunate tendency to
catastrophic failure in the first blow. To hold the all-EPS designs together better, Pro Tec introduced two or three
years later an all-EPS helmet with internal reinforcing. Their Mirage model had a nylon mesh inserted in the foam,
clearly visible in the vents.
The mesh is visible in the vents in the second photo above. It
worked well, and has been followed by thousands of other designs using internal reinforcing to hold the foam together.
The early ones, including the Pro Tec, still had cloth covers and no outer shell.
The next big design step appeared about 1990 with the reintroduction of a shell to cover the EPS, this time in PET
(milk jug plastic) and other thin, tough plastics. The shell helped to hold the foam together in an impact and lowered
the sliding resistance of the helmet to make it skid more easily on pavement, both important safety features. In just a
few years this thin shell design took over the market, replacing both the remaining hard shells and the cloth-covered
EPS-only designs. The shell was produced separately from the interior foam, and then glued or taped on. Another innovation in the early 1990's was molding the foam in the thin
shell, by placing the shell in the mold first, then expanding the EPS bead to fill it. The heat of the process then
requires a higher grade of shell than PET, usually a polycarbonate, since PET will melt at the temperatures in the mold.
The technique fills the shell completely, with no gaps between the foam and shell unless there are quality control
problems.
That permitted the designer to produce a more protective helmet
with the same thickness.
Designers quickly found that the same
technique permitted them to thin the helmet down for more appealing styling and to open up more vents.
In the years since 1990 some manufacturers have continued making the hard shell, mostly in ABS plastic. Most of their models are for skate-style helmets only, where the style endures. In 2001 a company called Hopus Technologies / Aegis Helmets managed to develop a technique to make molded-in-the-shell helmets using an ABS hard shell.
At about the same time as thin shells, manufacturers added a supplemental stabilizer in the rear of many models in the form of a plastic patch or cloth strap in the rear to hook below the bulge in most riders' heads (the occipital bone) and hold the helmet on better. Many innovations in these stabilizer designs have followed.
The most efficient shape for a helmet in a crash resembles a bowling ball. Round, smooth surfaces slide well and
"scrub off" energy from a crash, while avoiding any tendency for the helmet to snag and jerk the rider's neck. This has
been demonstrated in lab tests. But designers began flogging "aerodynamic" designs in the late 1980's as the aero craze
peaked. Greg LeMond wore one in a famous time trial where he came from behind to win the Tour de France. Bicycle helmet
shapes have become elongated ever since, basically as a fashion trend, since the aero quality of the helmet has no real
effect at the speeds most riders travel. An unfortunate trend in
shapes became evident in the late 1990's as designers began producing helmets with ridges, rear projections and
squared-off lines to give them a more stylish appearance. We have ranted against the trend, but without much effect, and
have been unable to get provisions in any standard requiring low sliding resistance. We could only hope the fashion will
reverse as fashions always do, and lead us back to smoother designs. Finally in 2004 there were signs of at least a few
rounder, smoother designs produced for the "commuter helmet" niche in the market. Bell introduced the Metro, followed
quickly by a number of others.
The Metro was an intentionally clunky
design, but SixSixOne found a design in China shortly thereafter and brought the helmet on the right below, the Allride,
to the US market. Weak marketing doomed it to low sales, and the company dropped it from their line after 2005. But the
original producer brought it back for 2006 as the Vcan VCK37 (on left below).
In 2006 the round helmet trend advanced in Europe with the introduction of the CASCO Warp II helmet, a very
round and smooth design for track racers. The manufacturer advertises it as a more aerodynamic design based on automotive
research. Track racers in the UK were early adopters and their demand alone led to backorders for the helmet. It is not
clear why the aerodynamic claim led buyers to reject all of the aero research of manufacturers of the elongated
designs.
The extreme of the elongated aerodynamic style is the chrono helmet developed in the 1980's for Olympic time trials. This one has a rounded front and usually has a very long tail that rests on the riders back when in the tuck position used by time trial riders. Vents are minimal or non-existent. Early models had only a shell without impact protection, but in 2002 Louis Garneau introduced one that met the requirements of the US CPSC standard, and various manufacturers soon began making them to the European CEN standard. We have a page up on current chrono helmets.
Another major helmet shape that crept into bicycle helmets is the "skate-shaped" helmet. Originally developed for
skateboarders by Pro-Tec, the style has lower rear coverage, small round vents in the front and even smaller round vents
in a circle on top. The skate style helmet is almost always a hard
shell with ABS plastic. Although originally using a squishy rebounding foam that provided the multi-impact performance
needed for aggressive skateboarding, the helmets evolved into bicycle helmets because the squishy foam would not perform
in harder impacts called out by bicycle helmet standards. After 1999 when the CPSC standard came into effect, big-box
retailers were not willing to put a helmet on the floor that could be bought as a bike helmet but did not meet the CPSC
standard. As a result, most skateboarders now are buying single-crash bike helmets with crushable EPS foam inside.
A few manufacturers are making helmets with EPP foam or other foam that can be certified to
both the ASTM skateboard helmet standard and the bicycle helmet standard.
Liners
Until the 21st century, bicycle helmet liners were all crushable foams. In the late 80's or early 90's came
the introduction of new foam types to replace the simple EPS picnic cooler foam that dates from the 1950's. One of the
first was EPP, Expanded Polypropylene, a foam that looks much like EPS but has a slightly rubbery feel. It is extensively
used in the automobile industry. EPP has the desirable characteristic of slow return to its original shape after an
impact, and is therefore well suited to multi-impact helmets. It is generally considered to have slightly more rebound on
initial impact than EPS, and a little less impact attenuation for a given thickness. Although Aria Sonics had an EPP
helmet for five years or more, the design was never appreciated by consumers, and its marketing was inadequate to
establish its advantages. A Canadian company called Headstart introduced EPP designs in the mid-1990's, but the helmets
were not well finished and did not have the quality appearance that was required to sell in the U.S. market by that time.
In the early 1990's an advance in EPS from General Electric called GECET was introduced to bicycle helmets. Although GE had not originally designed its combination foam and resin product for bicycle helmets, it was appreciated for its resistance to catastrophic failure, permitting manufacturers to open up larger vents and thin out liners in some places.
Another foam introduced in the 1990's was Expanded Polyurethane, or EPU. This is a slightly heavier foam with
exceptionally small and uniform cells. It skins over in the mold, producing a shell-like cover on the lower section below
the regular plastic shell. EPU can be inmolded or the shell can be applied
afterwards. It has almost no rebound and performs well in lab tests. Taiwanese manufacturers are the main users of EPU,
and helmets made of it are among those on the Snell B-95 certification list, indicating that they perform well indeed.
There may be some environmental issues related to the production process for EPU, however.
In 2001 a ski helmet company known as Team Wendy or W Helmets showed a new helmet with a foam they call Zorbium.
The company claims it has extraordinary energy management
capabilities, with a "rate-sensitive" quality that makes it give in a lesser impact but causes it to stiffen to handle a
harder hit. Although the concept is apparently sound, we never could get any test data on production models. The foam is
heavy and absorbs sweat readily. W Helmets remains the only user of this foam, and their implementation has been directed
toward ski models. By 2010 they were no longer making civilian helmets.
It may seem surprising that most bicycle helmets are still made of the EPS developed in the 1950's. Over the years we have heard of various experimental foams that were about to break open the market with astounding performance characteristics, but few have materialized in actual production, and their benefits are not readily apparent. There are probably limits to such properties as foam thickness. Basic laws of physics make it evident that it would be very difficult to stop a rider's head from 14 MPH to 0 MPH in less than, say, a half inch of crush space, without exceeding the 200, 250 or 300 g limits in bicycle helmet standards. So better foam may not produce much improvement unless the crush rate of the EPS has some undesirable characteristics or multi impact is important for the sport. Thicker helmets could do more, but consumers reject them. Some attempts have been made to improve the way EPS works, mostly with dual-density formulations. The cone-head technology developed by Don Morgan and marketed in 2010 is designed to make the transition between layers smoother.
In the years since 2000 several newer foams have appeared, associated with marketing labels like "Brock foam," or "cross-linked foam." The latter has been rumored since well before 2000. Pro Tec has SPX foam, a different formulation of EPP, and other companies are using TAU or Re-up foam, again different formulations of EPS or EPP.
Beginning about 2007 with Cascade lacrosse helmets, liners appeared that were not foam-based. Most depend on plastic
constructs of some kind that manage energy by collapsing on impact. They showed up first in football and lacrosse
helmets, but in 2014 there were production bike helmets with Koroyd [tm] liners that look like bundles of soda straws.
They still had EPS molded around them. At about the same
time, the first helmet using an EPS/Corrugated board liner appeared, marketed for a time by Abus. Non-foam liners have huge potential for future development.
In 2019 a UK company called HEXR began shipping 3d printed helmets. They produce custom helmets with a 3D printed liner
of hexagonal honeycomb cells that crush on impact. The interior liner is custom made for the wearer's head, using data
from a head scan done with an iPad or iPhone that can be done at home.
HEXR claims their helmet provides better energy
management than a foam helmet, but cites only one European standard lab test at an average of 144g, a level that is good
but can be attained with a good standard thick EPS foam liner. In theory, a custom helmet can use all of the available
space between your individual head and the inside of the shell for energy-management liner, so this technique could be
the future of high-end helmets. For uniquely shaped heads or those with cochlear implants that alone could be a big
advance.
The HEXR is certified to the European EN1078 standard, so will not be available in the US market until a CPSC-certified
model is developed. The HEXR sells for £300, including the head scan. For comparison, the only custom 3d printed
football helmet currently on the market sells for $1700. The easily-managed head scan raises the possibility that
manufacturers of conventional off-the-shelf helmets could match individual head scans done at home or in a shop with the
interior dimensions of their helmets to provide best fit recommendations at a fraction of the price of a custom helmet.
For those who must buy online that could be a big advance.
In 2021 Kav Sports launched a Kickstarter campaign to produce a new 3D printed helmet meeting the CPSC standard. KAV already had a hockey helmet on the market. Their product is now available. They fit the helmet with a "fit kit" that lets the user take measurements, not with a scan, and provide a test cap to check the fit before manufacturing the helmet. We were impressed in 2024 by lab test results on the KAV.
We have a page up on helmet liners if you want more detail.
Buckles and Straps
The basic bicycle helmet strap was made of nylon beginning with the early MSR and Bell designs. In
the late 1990's other materials including polypropylene replaced some of the nylon, but the resultant strap is difficult
to distinguish from nylon. Each formulation has its own characteristics, affecting such parameters as buckle slippage.
The first fasteners were mostly D-rings, a design borrowed from motorcycle helmets where the strap is fed through two
d-shaped rings and doubled back through them to grip. This is done each
time the helmet is put on. Making the rings from stainless steel ensures resistance to corrosion from sweat. This design
is simple, very strong, reliable for a decade or more of use and ensures that the rider can achieve optimum tightness on
every wearing. But many bicycle riders find it fussy and sometimes difficult to fasten, and triathletes complain that it
takes two hands. Instead, manufacturers turned to plastic buckles of many designs, dominated by the design produced by
Fastex using a male two-prong buckle sliding into a female mate with side-squeeze release achieved by pressing the two
male prongs together.
Strap junctions and other fitting pieces
for helmet straps have advanced from flimsy plastic parts or simple sewn connections to much more elaborate fittings to
facilitate adjustment. Some have cam locks or other means of locking the strap when adjustment has been achieved. Most
have a "strap creep" problem, resulting in loosening of straps with repeated use. This can sometimes be limited by adding
rubber rings to grip the strap where it enters the fitting. Although fitting a helmet well is critical for good
performance, no manufacturer has yet produced a helmet that is self-adjusting when first worn. That is perhaps the
greatest bicycle helmet advance waiting to be made. After all these years of bicycle helmet use, fit is still our biggest
problem.
Other Design Features
Since foam is a superior insulator and heat is a problem for cyclists, vents have been a
feature of almost every bicycle helmet since the earliest hairnets. There have been attempts to design for air flow in a
space between helmet and head, as construction hard hats are made, notably the Bailen Bike Bucket from the 1970's.
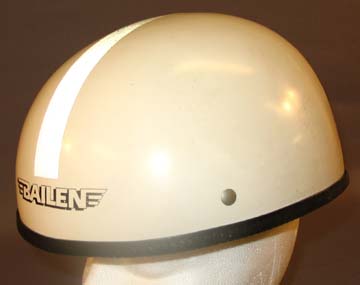
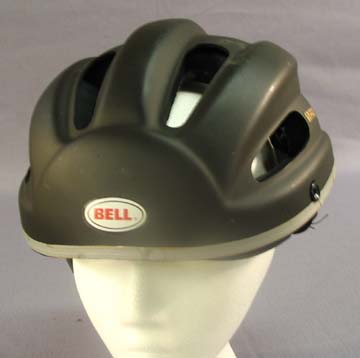
Women and children have not been neglected in helmet marketing, although aside from graphics the only women's feature of note is the pony tail port, pioneered by Troxel in the early 1990's after one of their designers was annoyed that standard designs failed to give enough space for his ponytail. In ensuing years many helmets and rear stabilizers came to be advertised as "pony tail compatible." Some actually are.
Child or toddler helmets have typically provided extra coverage and have often lacked vents. Some are equipped with buckles designed to minimize pinching the skin while buckling.
Helmets for very large heads have evolved as well. Riders with larger heads had great difficulty finding a
helmet larger than 7 7/8 in the early years. In fact the American head size crept upward throughout the 20th century, and
heads large than that size are not as rare as they once were. The Bicycle Helmet Safety Institute urged manufacturers to
make an extra-large helmet, but most saw it as unprofitable. Despite that, Bell brought out their Kinghead in 1998 as a
service to those who needed it rather than a profit-making venture. It was the first bicycle helmet designed uniquely for
riders with extra-large heads. The Kinghead fits up to size 8 1/4,
and can be turned sideways on most smaller heads. Bell has since dropped the Kinghead from their catalog, although
dealers can still order them, and replaced it with the slightly smaller model. Other manufacturers have now begun
producing larger models as well, and we have a current listing on our page of helmets for larger
heads.
Fitting pads in helmets are another design feature that in early years were neglected but have received more attention in the 1990's. MSR led the field in its first model, featuring a suede-covered thick cotton sweatband that was hook-and-loop mounted in the helmet. It has not been duplicated or equaled since in comfort or sweat control, although pad foams and coverings have advanced through the years, and many high tech materials are now touted as features of higher-priced helmets.
Reflective helmets and accessories are another niche market. Many riders who ride at night believe that reflective outer surfaces add safety to a helmet used by a rider after dark on roads with cars. Studies done in the mid-1990's by CPSC have challenged that belief, indicating that drivers do not see or identify cyclists earlier when there is reflective tape on the helmet. Over the years, helmet manufacturers have provide little or no reflectivity in their designs. Consumers who ride at night, including notably those who commute to work, often do add reflective tape to their helmets. Subjectively it appears to enhance their conspicuity, leading me to question the CPSC study results.
Lights are another and more aggressive means of increasing conspicuity of those who ride at night. Helmet-mounted headlights are favored by some riders, particularly for off-road trails where aiming the light with head movements can illuminate a trail twist that would just be shadow with a rigidly mounted front handlebar light. On the street, these lights can be flashed in an oncoming driver's face, or the eyes of another trail user. This partially blinds the driver or trail user for some period until their eyes readjust. Helmet lights are usually light and compact. Any helmet light must have a mount that lets it break away easily to avoid jerking the rider's neck in a fall or contact with a tree limb. The technology of helmet lights has evolved, with LED and HID light sources replacing older incandescent bulbs. Batteries to power them are usually rechargeable, and have evolved from NiCd to NiMH and Lithium Ion technology for higher energy density.
Mirrors are a necessity for bicycle riders on roads, just as they are for any other vehicle on the roadway. They are seldom marketed with a helmet, but often are added on by the consumer after purchase of the helmet. Small helmet-mounted mirrors were made by hand by Chuck Harris and others since the 1970's, and in the mid-1980's several brands of mass-produced add-on mirrors appeared. They are best mounted with hook-and-loop, and in any event must detach easily in a crash to avoid jerking the rider's neck. Some riders continue to use glasses-mounted mirrors which were in use before helmets became popular, but these can cause problems in falls if the mirror mount rotates in the direction of the rider's eye. In 2004 Bell introduced an extra-cost mirror for their commuter helmets.
Sustainability
Helmets are notoriously difficult to recycle. We have a page up on what to do with your EPS-lined helmet, but there are few options. The French company Urge entered the US market in 2011 with bicycle helmets that are environmentally sensitive and in some cases linked to green causes in other countries. Some models use recycled EPS, and all have straps of recycled PET. Starting about 2015 US manufacturers began to talk about environmental impacts. The materials in the 3D printed HEXR helmet liner mentioned above are made from castor bean oil, a sustainable product. Giro for a time had a "Silo" model that had a liner constructed from cornstarch. But in general the industry is still far behind the curve on environmental impact.Conclusion
This summary will grow and be revised as we learn more. If you have additions or corrections to suggest, please email them to me.Randy Swart, Executive Director
Bicycle Helmet Safety Institute
Other Sources
Other good places to look for background on bicycle helmets in the 80's and 90's would include our newsletters from past years. They go back to 1983.For the definitive book on the history of every type of helmet including good coverage of bike helmets and a lot more, see Jim Newman's "Modern Sports Helmets: Their History, Science and Art." The author is a respected member of the helmet standards community and a biomechanician who has contributed to the advancement of injury analysis and the biomechanics of head injury. Here is the Amazon page on the book.
Here is another Newman
paper on helmet history, done in 2005 for IRCOBI.
For another scholarly examination of helmet history, see the article on the Snell Memorial Foundation site titled
Helmet Development and Standards. It was written by Ed Becker, their Executive Director
and another long time contributor to helmet standards development.
Back to the top
Back to the Home Page